Mechanical Seal Design, Operation, And Maintenance Problems
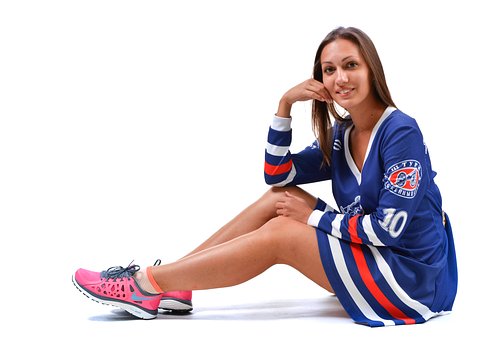
Share: In my seminars I teach that mechanical seals fail prematurely because:
The lapped faces open. A seal component becomes damaged. In the following paragraphs we will learn how these failures can be separated into:
Design problems.
Operation problems.
Maintenance problems.
These individual subjects have been discussed in other sections of this Technical Series. The purpose of this paper is to give you an overview of the subject, and assist you in your troubleshooting function.
MECHANICAL SEAL DESIGN PROBLEMS
Problems with the Seal Faces:
Wrong carbon or hard face selected. The material is not compatible with the fluid you are sealing, and the cleaner or solvent used to clean or flush the system.
Face flatness problems:
The face cross section is too narrow causing temperature or pressure distortion problems. The material modulus of elasticity is too low. The face is not hard enough. All clamping forces must be "equal and opposite" to prevent face distortion. In many designs they are not. The differential expansion between the seal face and its holder can cause the face to go out of flat.The faces were not lapped at a cryogenic temperature and the seal is being specified for cryogenic service. Bad packaging.
Poor heat conductivity:
Carbon is a poor conductor of heat compared to most hard faces. Many ceramics are not good conductors of heat . Plated or coated faces can "heat check" due to a differential expansion rate between the coating and the base material. The seal face is sometimes insulated by a gasket or elastomer. Low expansion steel face holders are not usually corrosion resistant.
No vibration damping has been provided to prevent "slip stick" vibration problems. This is a major problem with metal bellows seals.
Unbalanced seal designs require excessive flushing or cooling to remove unwanted heat. The carbon must be dense enough to prevent entrained air pockets from expanding and causing pits in the carbon face. An "unfilled carbon" with four impregnates is the best.
The Springs or bellows.
Springs in the fluid can clog easily, especially the small springs. Stainless steel springs and bellows are sensitive to chloride stress corrosion problems. A single spring can be wound in the wrong direction. Thin bellows plates and small cross section springs are sensitive to abrasive wear. Rubber bellows experience a catastrophic failure mode when the bellows ruptures.
Stressed metal corrodes faster. Springs and metal bellows are subjected to high stress. Too much spring or bellows movement will cause an early fatigue of the metal.
The Dynamic Elastomer (the one that moves)
Some elastomers do not move to a clean surface as the face wears. Spring loaded elastomers stick to the shaft or sleeve and are sensitive to the shaft diameter and finish. Elastomers positioned in the seal face are subject to the heat generated between the seal faces. Dynamic elastomers are very sensitive to the shaft tolerance and finish.
Operating conditions too severe for the design.
Elastomers and some seal faces are sensitive to temperature extremes. Excessive pressure can distort seal faces causing them to go out of flat. Excessive pressure can cause elastomer extrusion. High speed can separate the seal faces in rotating seal designs. High speed can cause excessive heat at the seal faces. Excessive shaft movement separates faces also. Hard vacuum can "out gas" an elastomer causing it to leak. Dual seals
Rotating "back to back" designs:
Centrifugal force throws solids into the inner faces. Inner seal blows open if barrier fluid pressure is lost. Inner stationary face is not positively retained to prevent movement if the pressure is lost between the faces. When the outboard seal fails the inboard will fail also due to the pressure drop between the faces. The inner seal has to move into the sealing fluid as the face wears. This is a major problem if the fluid contains solids. Failure to use "two way" hydraulic balance causes the inner faces to open with a reversal in barrier fluid pressure.
Design problems that cause excessive shaft movement
An elbow is installed too close to the pump suction inlet. The mass of the foundation is not five times the mass of the pump and its driver. Wrong size pump was specified because of safety factors and, as a result, the pump is operating off the B.E.P.
The pump was selected oversize in anticipation of a future need. A "centerline" design should have been selected when the operating temperate exceeded 200F (100C). The shaft L3/D4 is too high. The pump is cavitating due to a design problem.
Too high a N.P.S.H. is required. You need a double suction pump. The suction specific speed number is too high. You are using too low a specific speed impeller. A reducer has been installed up side down, letting an air pocket into the suction. The impeller to cutwater clearance is too low. There is too much suction resistance due to excessive piping. Too much suction lift for the fluid temperature.
Other design problems
Some seal designs cannot compensate for thermal shaft growth or impeller adjustment. Cartridge versions are needed for this feature. The pumping fluid is located at the inside diameter of the seal faces. Solids will be thrown into the lapped faces destroying some face materials.
Solids will pile up in front of the movable faces, preventing them from compensating for wear.
Most mechanical seal faces are weak in tension. Hysteresis (delay) problems caused by the seal mass and sliding elastomers. Poor packaging that allows face damage during shipment and storage. Designs that frett (damage or groove) the shaft or sleeve. High speed requires the use of stationary seal designs. Centrifugal force can open rotating designs above 5000 fpm. (25 m/sec.) The seal is positioned too far from the bearing housing. Lack of a self-aligning feature is causing excessive face movement. A tapered stuffing box can cause face damage. No vent has been provided to vent the stuffing box in a vertical application. Hardened shafts and sleeves can cause the seal set screws to slip. A discharge recirculation line is aimed at the lapped faces, causing them to wear, and interfering with the seal movement. Problems caused by the product you are sealing.
by: Angela
Types Of Personal Injury Cases A Personal Injury Lawyer Can Handle Decor Condos With Led Light Christmas Wreath Feel Free To Conduct Search By Ssn Through Online Search Engines Paradise Punta Cana Top Ranked Trip Guidelines Villas Promos Dining And Sights Footie Boy Pajamas Keeps Your Young Men Warm Warning - Dieting is Not the Fastest Way to Lose Weight Baking for Today by Betty Crocker Review Interesting Fancy Dress Ideas & Styles What To Look For When Buying Forced-air Warming Devices Tips On Obtaining The Ideal Business Insurance Plan For Your Organization Wedding Photography Hampshire The Allure of Designer and Discount Designer Clothing How Cancer Affects Those Around Us