Cross Country Bar Mill Control
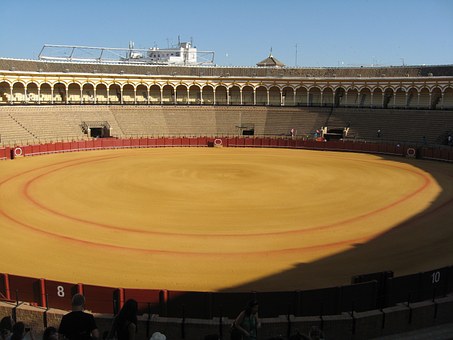
Share: Cross Country Bar Mill Control
Cross Country Bar Mill Control
Cross Country Bar Mill Control
By Steve Swan & Bernardo Sainz
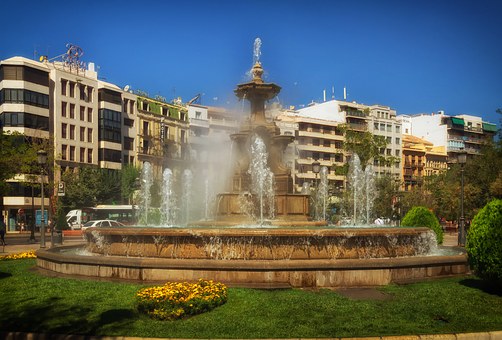
Share: http://www.amige.com
Abstract
This paper describes how Nucor Steel Marion, Inc (former Marion Steel Company) improved Rolling Mill yield and productivity by 20% and 10% with less than one million dollar investment in 2004. Three factors increased mill yield: less cobbles due to a better and more robust master control, less amount of bars lost during product changes due to better mill setup, and less waste material due to improvement in flying shear cut precision.
Productivity improved as a result of increased mill uptime due to less operational and maintenance delays as well as a secondary effect of yield improvement. The project included several challenges: to integrate a new coordinated control system to improve mill availability with minimum investment and making maximum reuse of a variety of old equipment and technologies.
Introduction
Nucor Steel Marion, Inc. is a division of Nucor Steel meaning that they share the same business philosophy, which focuses on taking care of customers by being the safest, highest quality, lowest cost, most productive and profitable steel company in the North America.
Nucor Marion manufactures a full line of specialty steel products in the specific shapes needed for the highway, construction and agricultural industries. The company also specializes in rebar, merchant rounds, breakaway Uchannel, small and midrange signposts, delineators and cable barrier systems.
In order to serve the concrete construction industry, Nucor Marion manufactures reinforcing bar. The breakaway Uchannel systems for small and midsized highway signs exceed crash impact standards by over 200% and they utilize newbillet steel that has 25% greater tensile strength and costs up to 50% less.
Combining these features and the current quality standards of a plant like this, there were several variables that were faced in order to provide the best control system from the furnace automation and billet tracking through the complete revamping of the master control of the rolling mill and cooling bed.
Scope of the Project
According to the standards of the company, their system was required to meet the functional control requirements through the integration of coordinated drives and control system. Overall performance requirements are based on the user's business needs as they relate to production, quality, reporting and system availability.
Marion Steel and AMIGE worked closely to define and agree on the systems that should be upgraded in order to maximize the costbenefit relation. The extensive knowledge of the process variables and best rolling practices by Marion Steel personnel were enhanced with state of the art control equipment and algorithms integrated in the very robust and open architecture of the system provided by AMIGE.
The basic system philosophy met the following requirements:
Enhance performance and reduce communication latency by customized structuring of the functional control to the mill configuration, including placing the functional control as close to the process and process sensors as practical.
Structure hardware and software so that each can be independently tested.
Minimize startup time by incorporating component simulation software into highly effective factory and field system simulations.
Extensive use of structured control blocks with friendly configuration tools.
Controller intelligence to directly generate diagnostics rather than requiring programmers to write dedicated software code.
Encourage production and engineering personnel to diagnose problems by extensive use of structured diagnostic messages available throughout the system.
Communicate process knowledge contained in the system directly to the operators with an intelligent combination of easily selectable graphical and alphanumeric screens.
Make available operating information, which allows user development of planned maintenance schedules and problem anticipation.
Minimize the quantity and type of dedicated communication networks and protocol.
Increased system reliability by implementing a flexible drive system that can be applied to a variety of applications.
System configuration
In order to give a brief description of how the system was originally configured, it is worth to mention that the Rough Section had a homemade PC based system to emulate a PLC, it also had some old Joliette analog drives and cascade control. In addition to this, the Rough and Intermediate Sections also had some Reliance PMI drives. For the Finishing section there were some ABB drives previously revamped with Reliance Front End and AB I/O to the ABB Master Control. A small GE 9030 PLC controlled the cooling bed.
New configuration was based on GE Innovation Series Controller (ISC) with a unified HMI and L1 system controlling all the way from the billet yard down to the cooling bed. Most of the drives were reused and only small ones in furnace, shears, pinch roll and cooling bed where replaced by new GE Innovation Series DC Drives due to economic convenience. The complete mill overview screen can be appreciated in Figure 1.
Figure 1: Mill Overview Screen
All reused drives were previously revamped by Reliance and equipped with Automax. In order to integrate those drives into the new control system Reflective Memory Architecture was used. This concept provides a very fast and efficient way of sharing data across distributed computer system since it is a high speed, realtime, deterministic network. With Reflective Memory each node on the network has a local copy of shared data. Writing to the reflective memory causes the The GE Fanuc reflective memory product that uses fiber optics with Fiber Channel technology was used in this case; Multibus for Automax and VME for the Innovation Series Controller. As a side result of this control system upgrade, the operator control desk was simplified and reduced. New operator station has only 3 PC with GE Cimplicity and smaller desk with a lot less manual controls.
Mill Setup
Product repeatability was increased by the use of a database for mill setup recipes; each product has its own recipe saved in the database for the operators to use. Also operators are able to adjust the parameters while running the mill with a particular product and then save it in the database as the "best practice" product recipe. This was possible as a result of the integration of the rolling practice with the new control system, a great effort between Marion Steel and AMIGE.
As set of production reports are also available, including mill performance and delays as seen in Figure 2.
Figure 2: Set Points
Master Control
By having a unified Master Control, Nucor Marion was able to improve mill availability and reduce cobbles. The Master Control is where the all the Mill parameters are converted into linear speed references for the stands. There are four main functions controlled in the Master Control: rolling modes and permissives, cascade speed control and cobble detection.
Rolling Modes and Permissives
The mill modes are Ghost Rolling and Real Rolling. Ghost Rolling feature is provided to be able to test the availability and operation of every master and auxiliary equipment along the mill prior to mill start up after a down time. These modes can also be switched using the Mill Overview screen. All the permissives are evaluated in order to enhance the value of the simulation. Operator screens and pulpit commands are fully operational while in ghost rolling mode. If any permissive is missing, the operator can easily locate the problem using the extensive diagnostic features provided by the system.
Stand permissives are grouped and managed so that, in some cases, a countdown will begin before the process is interrupted. This function enables operation to take the required action to avoid delays depending on the available time.
Cascade Speed Control
Based on Mill Set Up parameters like delivery speed, stand reduction factors, gear ratio and stand diameters, the speed reference set point is generated for every equipment. Operation has the ability to modify the stand speeds in two different ways. The first is to adjust an individual stand speed, this operation will modify the reduction factor of that stand and the downstream stand in opposite direction. The other, and most common way is to cascade the speed of all upstream stands in order to modify only the reduction factor of the selected stand. All automatic compensations like Loop Control manipulation modify stand speeds in cascade mode.
Cobble Detection
The cobble detection function provides detection of head end cobbles that occur in the mill. It utilizes HMDs and stand loads to detect metal presence and works on the principle that each detection should occur at some specific interval after the last detection. The system predicts the time interval based on the given stand speed. If metal is not detected as expected, then a cobble is declared.
Interstand Loop Control
The Finishing Mill is equipped with interstand loopers to assure there is no tension in the bar. The Interstand Loop Control algorithm was also written in the Innovation Series Controller, which has the ability to run high speed tasks. The control loop achieved the great robustness required in order to have a high performance and stability trough all different products and speed range. It also has the ability to learn, it saves the control loop manipulation for the next bar. By doing this, the algorithm maximizes product quality by minimizing response loop time after just a couple of bars of the heat.
Roughing Mill Interstand Low Tension Control
In the Roughing Mill there are no loopers. Operation is responsible to run each stand at the required speed, so there is no tension in the bar. This function is also accomplished automatically for a wide range of products. Once the Mill Set Up is accurate, the system can sense and evaluate load fluctuation in every stand. If the system senses an increase of load in particular stand, it would mean that the stand is pushing the material into the downstream stand. In this case, the stand speed would be slowly and automatically cascaded down until the situation disappears. The algorithm also works in the opposite direction as well, increasing the stand speed if the downstream stand is pulling the material.
Bar Mill Shears
Clutch and Brake shear control applies to both Crop and Flying Shear. Control is provided for Clutch Shear where the shear drive runs continuously at the product speed plus a lead adjustable speed.
The shear cutting cycle is initiated by closing the shear's clutch to bring the blade from a parking position and zero speed to cutting speed. After passing the cutting point the clutch will open and the break will close, stopping the shear again in parking position. Now the system will be ready for the next cycle.
The functions provided are:
Manual normal cut. A single cutting cycle will be initialized by the operator (Crop Shear and Flying Shear).
Automatic head crop. If this option is enabled, the shear will crop the bar's head at a previously specified length. This length is calculated using an HMD placed before the shear and mill stand tachometer pulses. An automatic trigger generated by the controller initiates the cutting cycle (Crop Shear).
Automatic tail crop. If this option is enabled, the shear will crop the beam's tail at a previously specified length. This length is calculated using an HMD placed before the shear and mill stand tachometer pulses. An automatic trigger generated by the controller initiates the cutting cycle. (Crop Shear).
Cut to length control. This function cuts the product into segments according to an operator preset length. The length is measured using a calibrated pulse train from the cut point or from the head detected by HMD (Flying Shear).
Hot Bed Optimization. By predicting the tail length at HMD 2, a tail cut can be taken at the Crop Shear when the diverter is deselected and this function enabled, with the purpose of eliminating tails at hot bed.
Continuous running for cobble cut (Crop Shear).
Cobble mode: cobble cut and divert sequence for cobble in hot bed (Flying Shear).
The symbolic diagram for the cutting cycle of the Clutch and Break Shear can be appreciated in Figure 3.
Figure 4: Block Diagram of the Shear System
The block diagram depicted in Figure 4 shows the different inputs and outputs of the shear system required to perform the different functions provided.
There are some characteristics of the clutch and break shear function that are worth mentioning. Depending on material speed at shear location, the cutting cycle is as fast as a couple tenths of a second. This requires the execution rate of the controller to be in the 1 ms range. Also, the on/off control implemented as blade position regulator is, by nature, not very accurate in comparison to what we can achieve in start and stop shears. Given the mechanical system limitations and as There is another shear in the system, the Chopping Shear. It works different from the other shears; it is only turning at a higher linear speed than the delivery speed. So, when the bar is diverted, it will be chopped into little pieces. For this cause, it is not a high performance application.
Furnace Automation
Another very important part of the project involved furnace automation and billet tracking. These functions were implemented after mill start up because they were not critical to avoid mill production and new system testing. However, they provide an important productivity increase by adding reliable automatic sequences from the yard pusher trough the peel bar as well as heat and billet tracking to enhance documentation and records.
Project Results
Mill start up curve was very fast and the increase in productivity was noticed very soon after the start up. The first production record was established as soon as two weeks after the new system start up. Given the very wide range of products, adjustments were made during the first weeks of production in order to make control algorithms robust and efficient given the different mill set up conditions. This was accomplished satisfactorily to the point that there is no need for control loop gain adjustments for the entire product range.
http://www.amige.com
MEXICO
AMI GE International
Blvd. Diaz Ordaz #402
Col. Rincon de Santa Maria
Monterrey, N.L.
T. +52 (81) 1001-4050
F. +52 (81) 1001-4051
BRAZIL
Av. Das Naones Unidas,
8501- 2 andar
Sao Paulo, SP, 05425-070
T. +55 11 3067 8639
T. +55 11 3067 8004
ARGENTINA
Blvd. Alvarez #150
San Nicols,
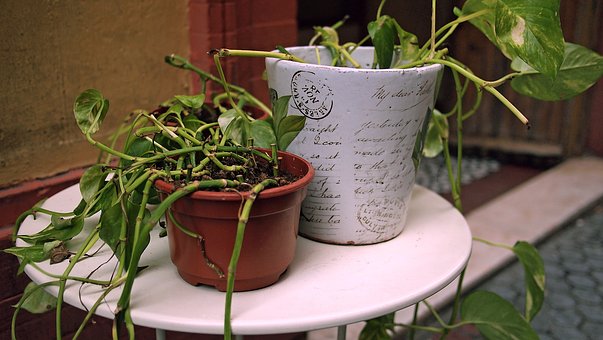
Share: Provincia de Buenos Aires
(B2900)
T. +54 93 461 665 222
http://www.articlesbase.com/industrial-articles/cross-country-bar-mill-control-2728811.html
Holiday Books Set The Mood For Holidays With Perfect Choices Looking For Cheap flights to Your Holiday Destinations Dollar From Australian Article Directory Christmas Miracle: Let's Make One - by Jorge Vargas Srilanka Tour And Travels - Explore Top Tourism Attractions Tourists To Buy Insurance, To Distinguish The "travel Liability Insurance", And Australia vs Ireland live Stream rugby stream sopcast Tv link||Live Rugby Gift Basket Ideas To Make Christmas Giving A Breeze Medical Tourism Destinations One Of The Most Popular Hen Do In London Laplands traditions at Christmas Autumn Dresses: How to Get the Latest Look of 2010 Quick Procuring Ideas for Holiday season